Challenge:
A 2012 case study on production of a biological drug in two 2000L stainless steel bioreactors would use >1 000 000L purified and Water for Injection (WFI) grade water, the latter valued ~ $250 0001 . This does not however mean that single use systems have conquered the market and there are still capacity and expense issues to be overcome. Stainless steel plant represents a major capital expenditure and is perfectly suited to the continuous mass-production of established, regulatory approved bioproducts in what is essentially a sunk cost. Therefore there will still be need for high volume water quality control in these systems. For other non-bioreactor based bioproduction systems such as hydroponic plant or filamentous fungus, the need for purified water may equal or exceed that of stainless steel plant. All of these systems need to monitor water quality at different parts of the process both as a dynamic component and as a waste product, whether process or cleaning related. Whatever analytical parameters are being examined under the fairly vast and disparate sources of regulatory policies the need for water analysis remains paramount.
Rationale:
Analytics in the bioprocess are currently performed by many legacy systems that have been established and regulatory approved over the last 40 years. Ideally this requires an entire analytical suite needs to be collocated, staffed and able to respond to disparate analytical tasks at any time point in that process. This must be on-demand and performed in a timely and regulated manner. To staff and equip such a fully functional lab would require large CapEx and OpEx (the latter including administration and consumables). Such a facility would serve to increase the dollar per dose ratio and decrease the chances of overall project investment. The need to limit the physical footprint of technology deployed in the process is paramount and so a multi-analyte technology that can look at water ions and ionic profile in production units as well as analyse amino acids and proteins would be optimal.
deltaDOT Solution:
The HPCE-512 has a small footprint and, being label free, has a very little consumable burden on operational budgets. The application of our LFII® technology offers increased data quality over more expensive systems with respect to reproducibility, resolution and quantification. Multivariant analysis of key bioreactor components and waste products on a single platform. deltaDOT’s HPCE-512 system offers a cost effective and rapid analysis of disparate components of any common expression system. This multivarient analysis can be demonstrated in the analysis of various ions detectable in water.
Figure 1 shows the detection of the metal ions of Cadmium in a water sample. Many metals, acids and salts, once ionized can be analysed by 1 Environmental and Financial benefits of single use technology www.ISPE.org 2012 capillary electrophoresis using indirect
detection where a background electrolyte that absorbs at 230nm is included in the separation buffer. When the ions separate they displace the background electrolyte causing an increase in the signal that can be measured by the photodiode array. shows the analysis of some common ions in a standard water sample. Figure 2 shows the analysis of some common ions in a standard water sample.
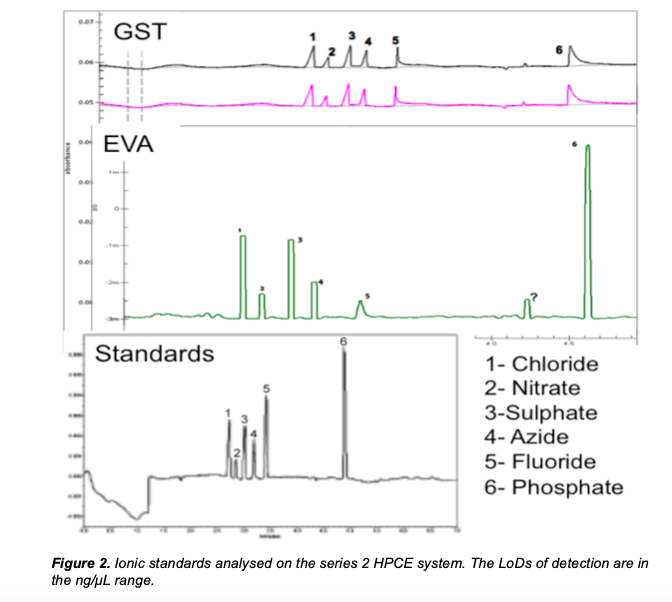
Commercial Applications:
The high quality data produced by deltaDOT’s HPCE can be successfully used as an alternative existing analysis techniques in many areas, as follows: –
• Rapid, cost effective multivarient analytics throughout the bioprocess
• Analyse water, acid and metal ions. Analyse protein quality upstream to downstream.
• Small footprint analytics for use in small mobile pod laboratories.
• Water effectiveness by ionic content in process development.
• Water quality in diverse production and purification unit processes.
• Water quality post clean-up, both ionic and protein content.
Further information For any additional information on our ability to characterise complex samples please contact us on info@deltadot.com